A wide range of welding processes is present across the different engineering sectors, mainly because they are suited to particular environments and materials. After reading this article, you will understand the 3 main types of welding, when to use them and how they differ.
If you have limited experience in welding, I suggest reading my other welding post first. It covers the basic terminology and fundamentals of welding.
MIG Welding
MIG welding stands for Metal Inert Gas welding and is a type of arc welding that generates heat from an arc between a consumable metal wire electrode and the workpiece metal. An electrode is simply an electrical conductor connecting a non-metallic part to a circuit. The heat generated from arcing results in the metals melting and join when cooling. A DC source is the power source for this welding process to allow a constant voltage.
The consumable electrode is fed through the gun, controlled by the trigger, unlike other welding techniques. As a result of this, MIG welding is easy to learn and is an attractive method for beginners. In addition to providing the consumable electrode, the gun also provides a shielding gas. The shielding gas prevents the weld from being contaminated by particles in the air. The protection provided by the shielding gas is crucial to producing a quality defect-free weld. The shielding gas also provides a smooth transfer of molten wire droplets to the weld pool, helping reduce weld splatter.

Although MIG welding is brilliant for beginners, it has its limitations. Only metals which have a thickness that is thin to medium can be MIG welded. Additionally, the weld produced is not controlled well compared to TIG welding.
TIG Welding
TIG welding stands for Tungsten Inert Gas Welding and has some similarities to MIG welding. The main similarity between the two is that they are both arc welding processes. However, TIG welding uses a tungsten electrode which is not consumable. As the electrode is not consumable, a filler material is manually added by the operator using their other hand to produce the weld material. Additionally, TIG welding uses an AC power source.
Like MIG welding, TIG welding uses a shielding gas to protect the weld from becoming contaminated from particles in the atmosphere. TIG welding works well on thin sections of steels and other metals like aluminium. Due to the added complexity of the process, TIG welding is much harder to acquire. Also, it requires an extra amount of time compared to the majority of other welding processes.
Stick Welding
Stick welding is the informal name for this process, but how it is most commonly known. Shielding Metal Arc Welding (SMAW), as more formally known, is an arc welding process that is manual utilising a consumable electrode covered in flux. Note: A flux is a compound that acts to purify and protect materials. This welding process does not use a shielding gas like MIG and TIG welding. This is where the flux comes in. The flux which covers the electrode melts and produces vapour in the process, acting similarly to a shielding gas. Additionally, the flux generates a layer of slag which also helps prevent weld contamination from the atmosphere.
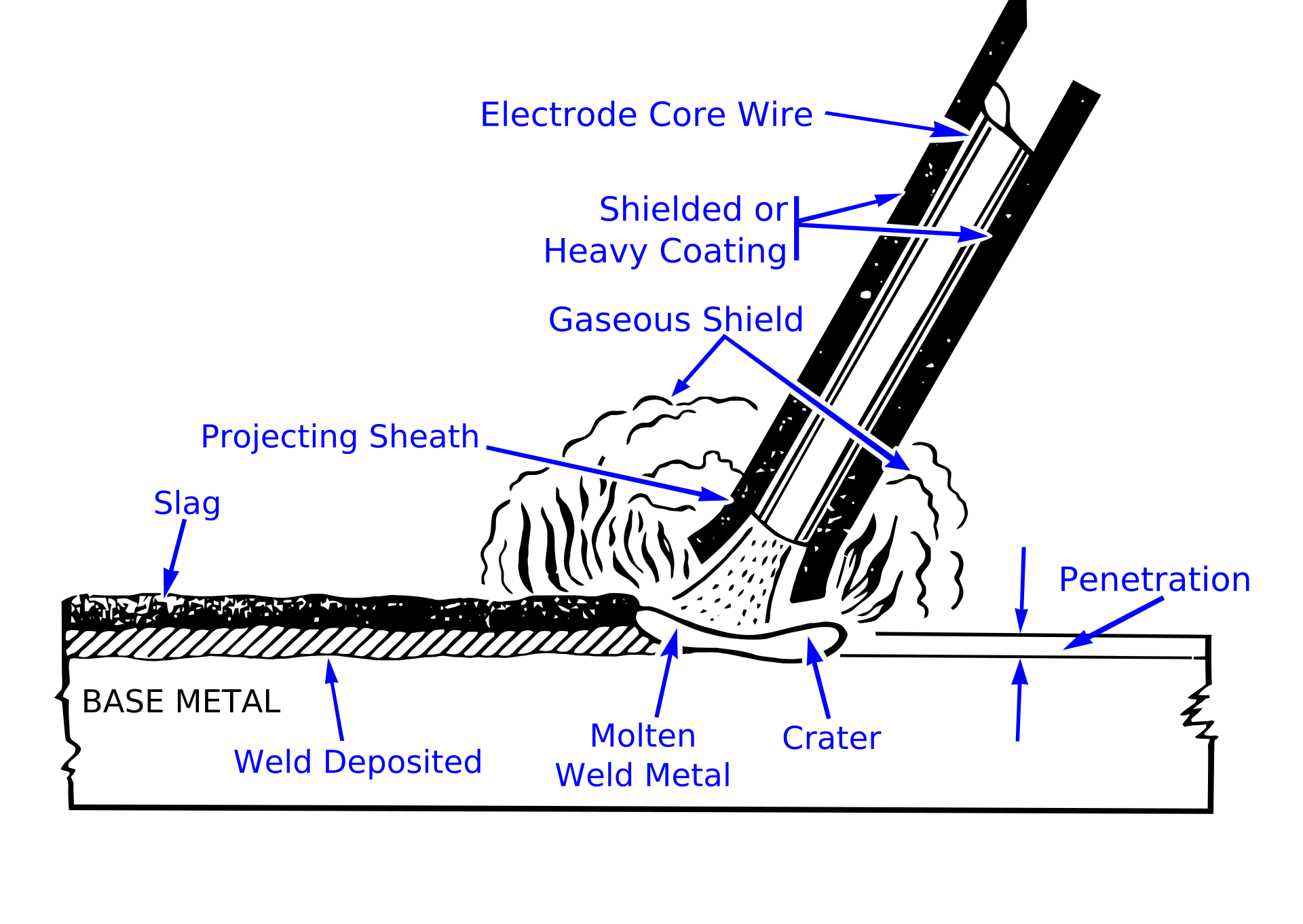
Stick welding is a simple welding procedure and proves to be favoured by those who weld outdoors. The primary reason for this is due to the welding process not being affected by external factors like wind due to not using a shielding gas.
However, there are disadvantages to stick welding. The process requires a greater skill level than MIG welding as the electrode must be held form a certain distance during the process. Also, a lot of weld splatter is a by-product of the process, making the surrounding area appear tarnished. On the other hand, unlike the previous methods, stick welding works off of either a DC or AC power source.
Summary
We have covered the 3 main types of welding used in engineering and are now able to state key differences between as summarised in the table below.
Welding Process | Consumable Electrode | Shielding Gas | Flux | AC | DC |
MIG | Y | Y | N | N | Y |
TIG | N | Y | N | Y | N |
Stick | Y | N | Y | Y | Y |
I hope you have learnt the key fundamentals of MIG, TIG and Stick welding and gives you a better understanding of welding processes overall.
Enjoy the post? Leave your feedback below
Related Posts: What is amazing welding, How to improve the fatigue life of welds